SRP Manufacturing Capabilities
Experience matters in precision converting, and SRP has achieved top-rated results since 1951.
Materials
Once we source top-quality materials from trusted brands, we then apply our unmatched manufacturing experience to convert pressure-sensitive adhesive, foam, sponge, rubber, and EMI/RFI materials into custom gaskets, seals and strips for a wide range of industries and applications.Manufacturing
Our manufacturing experience and depth of knowledge of how flexible materials respond to different manufacturing processes is why we are a 3M preferred converter. Some materials are more challenging to die-cut because of their thickness, density, elasticity or durometer. But our unmatched skill to prepare the best processing method enables us to achieve the exact dimensions you need.Efficiency
We also strive to keep material waste to a minimum. When we design a production plan to fabricate your gasket, seal or strip, we’ll select the manufacturing process that achieves exceptional quality and value, every time.Precision Die Cutting
Die cutting is the most common fabrication method for custom converted adhesive tapes and foam materials. Cut shapes from foam, pressure-sensitive adhesive, rubber, plastic and other flexible material with minimum concavity.

Benefits of die cutting
- The most cost-efficient for medium- and large-scale production runs requiring a custom fabricated die
- Easily cuts intricate designs
- Achieves tight tolerance ranges
Die-cutting methods
- Steel rules dies
- All-steel dies
- Compound and progressive tooling
- Feed-thru dies
- Cylindrical rotary
Commonly die-cut materials
- Adhesive-backed foam
- Adhesive-backed rubber
Die-cut applications
- Sealing Gaskets
- Electrical Insulation Gaskets
- Vibration Dampening Gaskets
- Adhesive-backed gaskets
Rotary Die Cutting
A custom metal die on a hydraulic press stamps out unique shapes from sheets and rolls of thin foam laminated with pressure-sensitive adhesive.

Benefits of rotary die cutting
- Makes through cuts with a single pass, with the option to make kiss cuts and perforations
- Efficiency for any size order with its rapid cutting action and high throughput
- Produces high-quality parts with consistency, achieves strict tolerance requirements
- Cost effective for small orders with less expensive tooling and dies
Commonly rotary die-cut material
- Thin Foams
- 3M Foam Tapes
- Film
- Pressure Sensitive Adhesive
Rotary die-cut applications
Adhesive-backed gaskets
Waterjet Cutting
Pressurized water from a computer-assisted nozzle creates clean cuts from foam rubber materials, making it the top choice for the projects where quality and fit make a huge difference.

Benefits of waterjet cutting
- Start production sooner since you won’t need to wait for custom die parts
- The final CAD file can be uploaded directly into computer software
- Achieves clean sharp edges and intricate designs without expensive tooling
- Exceptional at achieving narrow tolerance ranges
- Computer-guided nesting reduces material waste
- Capable of cutting materials up to 4” thick
- Frequently deployed for rapid production of prototypes
Commonly waterjet-cut materials
- Thicker and/or high-density foam up to 4″ thick
- Elastic material not supported by a liner
Waterjet-cut applications
- Thicker Materials
- High Density Materials
- Rapid prototyping
- Custom sized shapes
Laser Cutting
A software-guided laser beam cuts the shape with a high degree of accuracy.
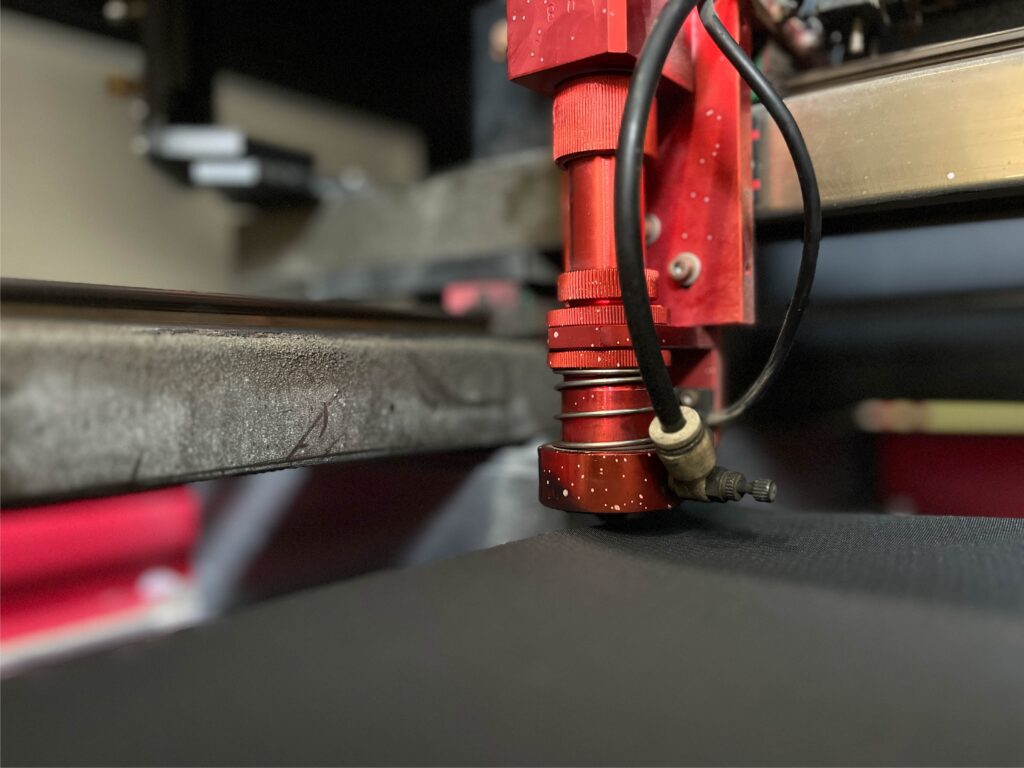
Benefits of laser cutting
- Minimize lead time because there is no custom-made die tooling required
- Creates intricate shapes and small parts with high accuracy, while meeting strict tolerance requirements
Commonly laser cut materials
- Thin Foams
- 3M Foam Tape
- Adhesives
- Thin Plastics and Films
Laser cut applications
- Rapid prototyping
- Sample parts
- Low-volume production runs
Automatic Slitting
Also known as bologna slitting and single-knife slitting, a single knife lathe slitter cuts a master roll of foam, rubber or adhesive tape down to the desired widths.

Benefits of automatic slitting
- Computer-guided rotating blade cuts strips of varying lengths from the same roll without retooling
- Achieves high throughput with minimal lead time
- Versatile: Cuts rolls of foams and adhesive material of varying thicknesses, widths and diameters
- No rewinding required, ensuring faster production and less production cost
Common materials for automatic slitting
- Rolls of foam with custom adhesive backing
- Rolls of rubber with custom adhesive backing
Automatic slitting applications
Custom-width tape rolls
Reciprocating Knife Cutting
An oscillating knife guided by computer software cuts shapes from chosen material.
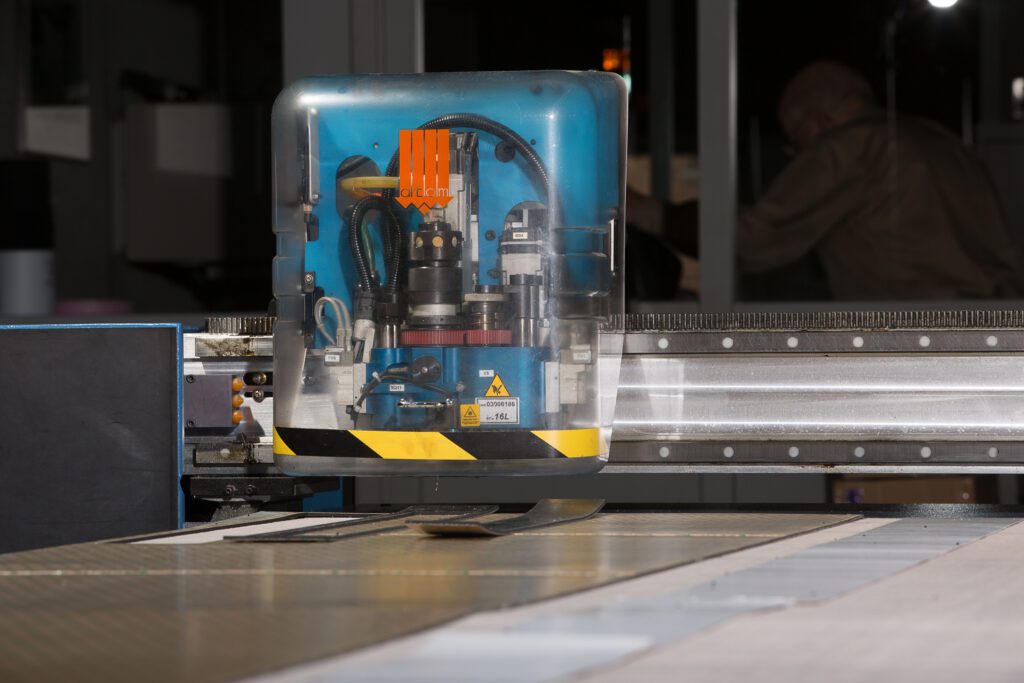
Benefits of reciprocating knife cutting
- Offers a range of versatile cutting methods including kiss-cuts, creasing, milling-routing, punching, engraving and angle cutting
- Produces intricate designs with high repeatability and clean finish
- Efficient production start with no custom metal die tooling required
- Interactive nesting software maximizes yields, minimizes waste
- Commonly used for rapid prototyping and product samples
Common materials for reciprocating knife cutting
- Foam
- Sponge
- Rubber
- Fabrics
- Foils
Reciprocating knife cutting applications
- Larger gasket shapes
- Rapid prototyping
- Product samples
Our manufacturing experience guarantees top quality parts, perfect fit, minimal waste and the best value for you. SRP has the expertise to recommend the most efficient methods that maximize the number of parts from your custom converted foam, rubber and adhesive tape.
How can we help?
Please submit the form and a member of our team will be in touch with you shortly